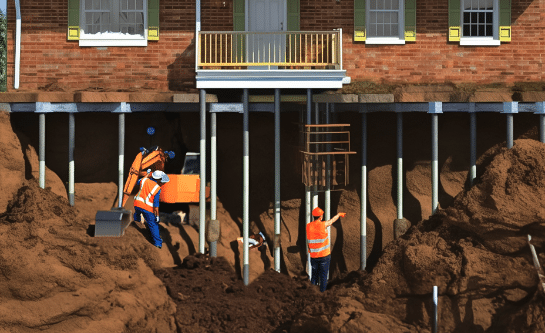
Foundation underpinning for treating subsidence
For properties experiencing subsidence, foundation underpinning is the traditional solution. But it’s not the only option.
Mainmark offers fast, non-invasive and reliable alternatives to foundation underpinning and solutions to common problems associated with ground movement or poor soil quality under residential properties, as well as commercial buildings – from factories and warehouses to offices, public buildings and social housing.
Our methods have been used on a wide range of structures, including multi-storey tower blocks, as well as car parks and roads.
Our Teretek® resin injection and JOG computer-controlled grouting techniques are rapid, non-intrusive and dependable ground improvement solutions that serve as effective alternatives to mechanical jacking. These methods address the root causes of subsidence, providing a comprehensive and long-lasting remedy:
- Ground improvement – Our methods increase the load-bearing capacity of the soil and mitigate liquefaction.
- Lifting and re-levelling – Through precise injection of resin or grout beneath the foundations, we gently lift and re-level the structure, restoring the property to a safe condition.
- Void filling – Our techniques fill voids within the soil, providing essential support to the foundation. This enhances the structural integrity of the foundation.
Our solutions are flexible and can be tailored to the unique demands of each project, delivering results that prioritise the safety and stability of commercial buildings and homes.
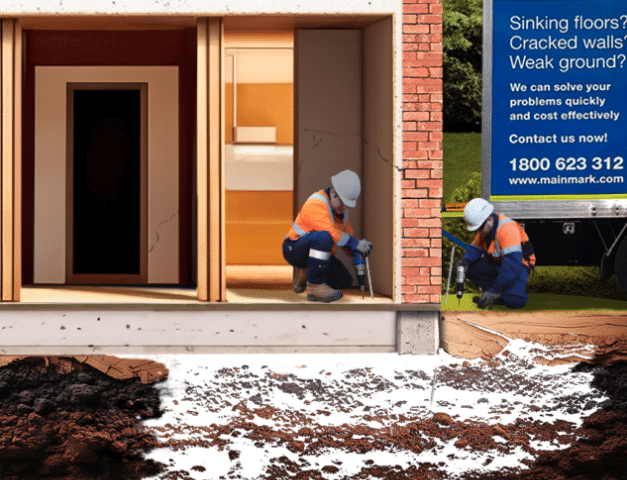
Is foundation underpinning the right choice?
For properties with subsidence, Mainmark’s solutions may be a better choice than traditional foundation underpinning.
Traditional foundation underpinning is a complicated, costly and disruptive project that aims to strengthen the existing foundations and involves digging out from under the foundations of a commercial building and then carrying out remedial works such as piling or filling the excavation with concrete and other fillers. This labour-intensive process can stretch over weeks or months, and during work, building occupants cannot be present. Often, heavy machinery or equipment may also need to be removed from the premises.
Mainmark’s foundation methods remove many of these complications while providing effective and durable results. Using surgical precision, we drill under the foundations and inject our proprietary materials into key locations. The process is:
- Quick – Work can usually be completed in one or two days.
- Non-disruptive – There’s no need to vacate the building and surfaces are immediately trafficable.
- Cost-effective – Mainmark’s solutions are less expensive than traditional underpinning and have fewer associated costs.
- Dependable – The environmentally friendly materials remain strong and stable underground, providing long-lasting protection against subsidence.
Foundation underpinning technologies
Mainmark foundation underpinning technologies
Teretek® – Resin injection alternative to foundation underpinning
Teretek® is an engineered solution for re-levelling subsided buildings that utilises a plural component, expanding polyurethane resin. The expansion force of the material results in the controlled lift of structures, with a by-product of localised bearing capacity improvement through soil densification and acts as an alternative to foundation underpinning.
JOG computer-controlled grouting alternative to foundation underpinning
JOG computer-controlled grouting uses a multi-point injection technique to insert cementitious grout materials under foundations that can act as an alternative to foundation underpinning. It can be used under commercial and residential buildings ranging from single-storey shops to high-rise structures. The injected materials have a controlled set time, which allows for the precise lifting of a structure.
Testimonials
We’re happy to have helped
Mainmark technology benefits
Benefits of Mainmark’s treatments for foundation underpinning
Fast
Our ground strengthening solutions can be completed within a matter of days or hours.
Immediately trafficable
Soon after work is completed, the area can be reopened to foot traffic and vehicles.
Non-invasive
Repairs are performed without the need for excavation or extensive disruption.
Cost-effective
Compared to other solutions, our technologies cost significantly less.
Environmentally inert
We use safe materials that are non-toxic and do not leach into the environment or affect the treated area.
Reliable
Our ground strengthening solutions provide long-term performance and protection for your investment.
Case studies
Featured case studies
Soil stabilisation FAQ’s
What happens with unlevel driveways, floors and hardstand areas?
After the application of the Mainmark solution, unlevel surfaces will become aligned again as the ground underneath is strengthened and re-supported. Simple cosmetic repairs may be required.
Will there be a mess?
Very little, if any. We use Teretek® engineered Resin Injection technology, which is likened to “keyhole surgery”, or JOG Computer-Controlled Grouting, with no major excavation and minimal disruption or mess. The injection holes required are very small.
How long does it take?
Each project is different and depends on the required amount of lift, area for correction, building construction, and ground conditions. Most projects can be completed in a day or two, and we can work at night or on one area at a time, so your business can keep operating.
Do i need to send my workers home?
No, most projects don’t require you to vacate the premises or even move furniture or equipment. For the most part, you can keep operating as normal. Driveways can often be driven on in as little as 30 minutes after treatment.
What warranty will i get?
The materials we use have been developed for use underground and have been specifically engineered to resist shrinkage and deterioration. Teretek® is warranted by Mainmark for an industry-leading period of 20 years.
Is it safe and environmentally friendly?
Injected Teretek® and JOG materials are environmentally inert and have no detrimental effects on the environment.
Talk to an expert
Get in touch about your project
Step 1
Please submit your enquiry using our online form. Please tell us why you’re reaching out so we can better assist you!
Step 2
One of our expert team members will contact you to schedule a site inspection that suits you.
Step 3
One of the Mainmark experts will visit your home or property, assess the damage, and ascertain the likely cause. They will establish the approach needed, creating a plan specific to the needs of your building and provide you with a detailed quote.
© 2025 The Mainmark group of companies. ‘Mainmark®’, ‘Terefil®’, ‘Terefirm®’ and ‘Teretek®’ are trademarks of the Mainmark group of companies.
Mainmark Ground Engineering (UK) Ltd.
CRN: 09372443